What is Porosity in Welding: Key Elements and Their Effect On Weld High Quality
Porosity in Welding: Identifying Common Issues and Implementing Best Practices for Avoidance
Porosity in welding is a pervasive problem that frequently goes unnoticed up until it causes considerable problems with the stability of welds. In this discussion, we will check out the key aspects adding to porosity formation, analyze its damaging effects on weld performance, and review the best methods that can be taken on to reduce porosity event in welding procedures.
Common Root Causes Of Porosity
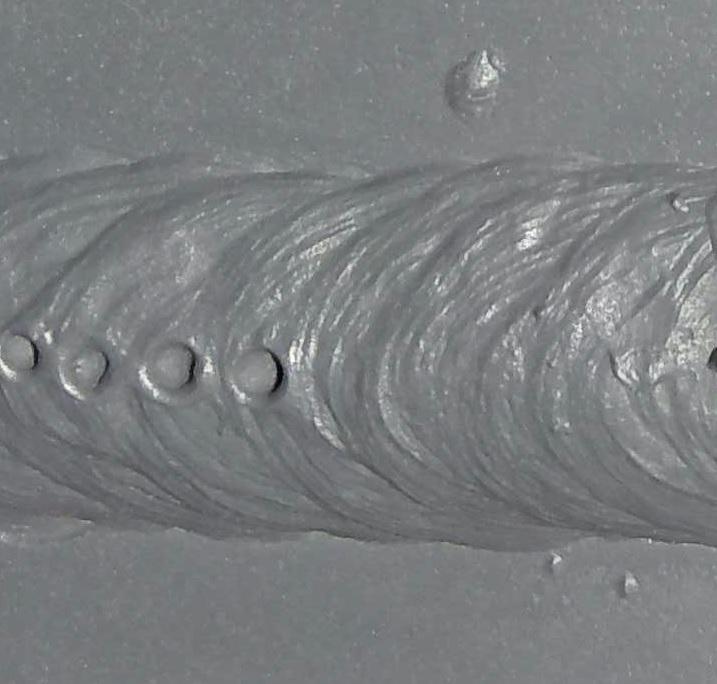
One more regular perpetrator behind porosity is the presence of pollutants externally of the base metal, such as oil, oil, or rust. When these pollutants are not successfully eliminated before welding, they can vaporize and become trapped in the weld, triggering flaws. Additionally, using unclean or wet filler materials can present contaminations right into the weld, adding to porosity concerns. To reduce these common sources of porosity, thorough cleansing of base steels, proper protecting gas choice, and adherence to optimum welding criteria are crucial techniques in accomplishing premium, porosity-free welds.
Influence of Porosity on Weld High Quality

The visibility of porosity in welding can considerably endanger the architectural integrity and mechanical residential properties of bonded joints. Porosity creates spaces within the weld steel, damaging its overall strength and load-bearing capability.
Welds with high porosity levels tend to exhibit reduced influence stamina and minimized capability to deform plastically before fracturing. Porosity can restrain the weld's capacity to successfully transfer pressures, leading to premature weld failure and possible safety and security dangers in vital structures.
Ideal Practices for Porosity Avoidance
To improve the architectural integrity and high quality of bonded joints, what specific steps can be carried out to decrease the occurrence of porosity during the welding process? Utilizing the right welding strategy for the specific material being welded, such as adjusting the welding angle and weapon position, can further avoid porosity. Routine assessment of welds and click here for more info prompt removal click here for more of any type of problems determined throughout the welding procedure are crucial techniques to prevent porosity and create top notch welds.
Relevance of Correct Welding Strategies
Applying correct welding strategies is extremely important in making certain the architectural honesty and top quality of bonded joints, building on the foundation of reliable porosity avoidance actions. Welding strategies straight affect the overall strength and resilience of the welded framework. One crucial element of appropriate welding techniques is keeping the proper warm input. Extreme heat can lead to raised porosity because of the entrapment of gases in the weld pool. Conversely, not enough warm may result in insufficient combination, creating possible weak factors in the joint. In addition, utilizing the appropriate welding criteria, such as voltage, present, and travel rate, is important for achieving audio welds with very little porosity.
In addition, the choice of welding procedure, whether it be MIG, TIG, or stick welding, should line up with the specific demands of the task to guarantee optimum results. Appropriate cleansing and preparation of the base metal, in addition to picking the best filler material, are additionally necessary components of i thought about this efficient welding strategies. By adhering to these finest techniques, welders can minimize the danger of porosity development and generate top quality, structurally sound welds.
Evaluating and Top Quality Control Measures
Checking treatments are essential to find and avoid porosity in welding, making sure the stamina and longevity of the last item. Non-destructive screening methods such as ultrasonic testing, radiographic testing, and visual evaluation are typically employed to identify potential issues like porosity.
Carrying out pre-weld and post-weld evaluations is also essential in preserving quality assurance standards. Pre-weld examinations entail confirming the materials, tools settings, and cleanliness of the job area to stop contamination. Post-weld assessments, on the other hand, analyze the final weld for any kind of flaws, including porosity, and verify that it meets specified criteria. Executing a comprehensive high quality control plan that consists of thorough screening procedures and assessments is paramount to minimizing porosity issues and making sure the overall high quality of bonded joints.
Verdict
Finally, porosity in welding can be a typical problem that influences the top quality of welds. By identifying the typical sources of porosity and executing finest techniques for avoidance, such as correct welding techniques and testing procedures, welders can make certain top quality and dependable welds. It is vital to focus on avoidance techniques to decrease the event of porosity and preserve the stability of bonded frameworks.